Single Stage Single Screw Extruder
Process: the bulk materials or thick flakes after crushed, conveyed into the single screw extruder by screw feeder, then, compressing, plasticizing in the extruder and removed the violatile and moisture by the vacuum system, after filtering through the filtration system to pelletize into granules. Depends on different screw diameters of single screw extruders, capacity can cover 100 to 1000kg/h.
In the anti-bridging silo, rotors keep the plastic flakes in motion. This prevents the flakes from bridging and ensures flowability.
In the transition area between the flake conveyor and the extruder input, the feeding screw acts like a feeder. The flakes are gently transported continuously from the large-dimensioned feeder screw into the extruder. This arrangement facilitates the processing of flakes of different sizes (the flake size is of minor importance). The pressure on the plastic flakes increases steadily as they enter the extruder intake, in order to achieve high throughput rates.
All the components are positioned in close proximity to prevent oxidation of the material and to make optimal use of heat from the shredding process.
Data of Single screw extruder | Throughput rate(Kg/hr) | |
Diameter of screw(mm) | L/D | |
80 | 33 | 120-160 |
100 | 33 | 260-350 |
120 | 33 | 330-420 |
150 | 33 | 450-560 |
180 | 33 | 650-800 |
200 | 33 | 800-1000 |
Double-stage single screw extruder
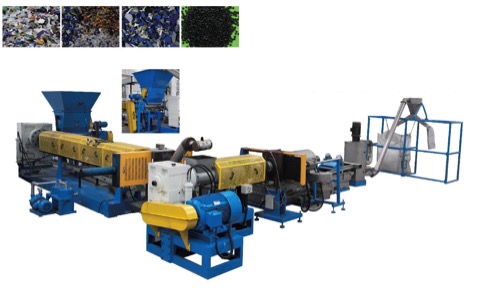
Applicable to:
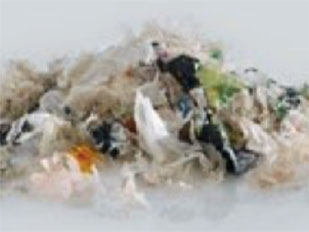
(washed PE film flakes)
In the case of washed post consumer film flakes (PE-LD, PE-LLD, PE-HD) the challenge lies in recycling with a high moisture content, which the materials have as a rule. Our double stage pelletizing line can release moisture perfect . , materials with up to 12 % residual moisture can be processed.
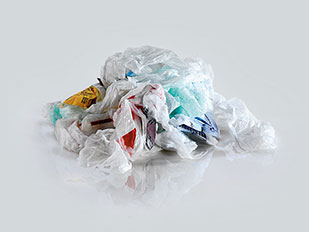
(PE or PP film with solid contamination )
In the case of PE or PP films with non-melting content such as paper, wood, aluminum, copper etc. the challenge lies in the required filtration performance. The conventional melt filtering technology on the market fails to meet these requirements in many cases. In order to fulfil these requirements XINRONG has developed continuously operating high-capacity filtering systems.
PE and PP applications:
• Carrier bags
• Packaging films
• Stretch films
• Agricultural films
Two-stage pelletizing system applied in the re-pelletizing job,which consists of two sets of single screw extruder, in case that recycles are with heavy dirty or required more output.
Features of two-stage re-pelletizing system:
1、Segmented filtering principle, fore filtering in the first extruder, and fine filtering in the second extruder, to reduce the frequency of filtering sieves changing.
2、Thanks to separated filtering system in two-stage extruder system can realize steady extrusion job.
3、Has one more volatilization between first and second extruder.
4、Second stage,s extruder can present low temperature extrusion, which can guarantee the final production,s quality.
Process: Two-stage regranulation line has input one more set single screw extruder in the second stage, it is most suitable to the processes, which require better filtration and higher capacity performance.
Depending on the type and quantity of the material the line can be equipped with a water ring, strand or underwater pelletizing system.
Diameter of screw(mm) | L/D | Throughput rate(Kg/hr) | |
First stage | 100 | 28 | 260-350 |
Second stage | 120 | 10 | |
First stage | 120 | 28 | 330-420 |
Second stage | 150 | 10 | |
First stage | 150 | 28 | 450-560 |
Second stage | 180 | 10 | |
First stage | 180 | 28 | 650-800 |
Second stage | 200 | 10 | |
First stage | 200 | 28 | 800-1000 |
Second stage | 220 | 10 |